Here are some of the most common questions that I am asking regarding building a home B-737 flight simulator:
Why a B-737NG and not an Airbus or other aircraft?
One of the first decisions that must be made when building a home flight simulator is what aircraft make and model. This is a critical decision. One must consider the availability of professional software applications for emulating the chosen aircraft. For example, Sim-Avionics is currently limited to the B737NG, B737MAX, B777, and the B787. ProSim is limited to the B737, B737MAX, and the Airbus A320.
A second factor is the availability of simulator hardware components that can be purchased for a specific aircraft make and model. With less popular aircraft types, the availability of flight deck hardware is more limited, difficult to find, and frequently more expensive due to the narrower market.
This simulator emulates the B737NG aircraft. It was chosen because the aircraft has been one of the most common single aisle aircraft built, with over 10,000 airframes built. It is one of the most popular types chosen for enthusiast home simulator builders.
What skills and equipment are needed?
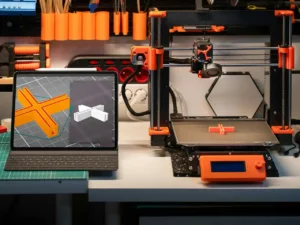
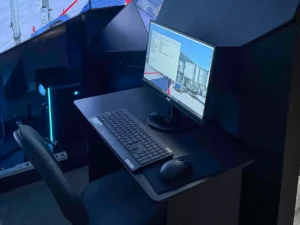
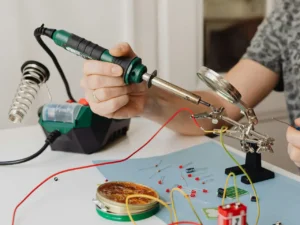
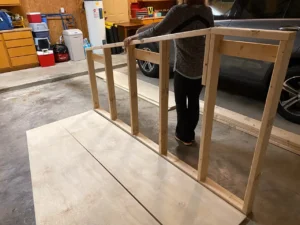
Basic woodworking skills are useful for building a flight deck platform base and the support framework for the external displays.
Most of the interfacing of the cockpit components is done with low voltage DC circuits. Being able to use a soldering gun, crimp wires, and troubleshoot with a multimeter will sometimes be needed.
A 3D printer is not necessary, but it can be useful for repair and customization of the flight deck. For example, I have used this for making an iPad holder that is mounted to the left of the captain’s crew seat. This allows me to use the iPad for reference to navigation charts and approach procedures emulating how this is done in real airline operations. I have also used the printer for overhead panel selector knob replacements, as well as various other minor flight deck components. I use Autodesk Fusion 360 for the 3D design software and a Prusa MK3 3D printer.
One of the most important things is to take the time to document the process. There will always be the need for maintenance of various hardware components. Computer networking and software configuration can initially be tedious and time-consuming. Documenting all the settings and procedures is extremely helpful for future maintenance and troubleshooting. I have created manuals for this simulator for various items such as setting up the computer operating systems and networking, configuration of MSFS 2020 or Prepar3D, external display field of view settings, ProSim737 or Sim-Avionics installation & configuration, etc.
Patience and the ability to troubleshoot is necessary. A home flight simulator is complex. It will require occasional troubleshooting and online research. It is not a simple plug & play device. Fortunately, there are many online forums used by enthusiast flight simulator builders.
How long did it take to build?
This simulator was built in stages, and continuously refined, over a two year period of time. If all the component parts were disassembled, it would probably take a couple of weeks for assembly, then another two weeks for the interfacing and computer setup.
Where can you purchase flight deck components?
There are many companies that manufacture flight simulator hardware components. There are more companies in Europe than in the North America. For builders located in the United States, this can add a substantial additional expense for shipping and US import duties. It can also be an issue for support when complex components require assistance or repair.
Some popular sources are: flightdecksolutions.com, flypfc.com, opencockpits.com, cockpitforyou.com, sismo-soluciones.com, cockpitphd.com, cpflight.com, simworld.aero, opencockpits.com, flightsimpm.com, and ledobodnar.com. A Google search can provide many more options.
Use of scrap real aircraft components is sometimes done. Some enthusiasts use real aircraft parts for most of the simulator hardware, including an actual aircraft flight deck shell. This requires significant mechanical and electrical skills. A popular site for used real aircraft parts is oncealoft.com.
This flight simulator uses Flight Deck Solutions for all the flight deck hardware components, except for the control yokes and rudder pedals. Flight Deck Solutions is based in Canada and has a strong reputation for making quality components and providing excellent customer support. For customers in the United States, import duties typically do not apply due to the USMCA trade agreement. Selecting one company for a home flight simulator can simplify things because the components are manufactured to work together and generally use the same interfacing paradigms and equipment.
One disappointing issue for home flight simulator enthusiasts is that some companies are transitioning away from the hobbyist/enthusiast market to the commercial training market. This shift is driven by the higher profitability of making simulator components for airline or pilot training companies. Also, commercial companies typically require less technical support than the private home hobbyist/enthusiast.
How to you know where to position the components?
There are published references online, such as www.markuspilot.com, that provide precise measures of the size and location of the components for the real B737NG aircraft. The real aircraft measurements were used for precisely placing the main instrument panel within the flight deck shell. Additionally, these measurements were used for installation of the other flight deck components such as the flight controls, pilot seats, etc.